The Scientific Research Behind Porosity: A Comprehensive Overview for Welders and Fabricators
Understanding the intricate devices behind porosity in welding is vital for welders and makers striving for impressive workmanship. As metalworkers look into the midsts of this phenomenon, they discover a world governed by different aspects that influence the development of these tiny gaps within welds. From the structure of the base materials to the intricacies of the welding process itself, a wide variety of variables conspire to either exacerbate or relieve the visibility of porosity. In this detailed guide, we will certainly untangle the science behind porosity, exploring its effects on weld top quality and introduction progressed methods for its control. Join us on this journey with the microcosm of welding blemishes, where precision meets understanding in the search of flawless welds.
Understanding Porosity in Welding
FIRST SENTENCE:
Assessment of porosity in welding exposes crucial insights right into the stability and top quality of the weld joint. Porosity, identified by the presence of cavities or spaces within the weld steel, is an usual issue in welding procedures. These voids, if not appropriately addressed, can jeopardize the structural stability and mechanical residential properties of the weld, bring about possible failings in the finished product.
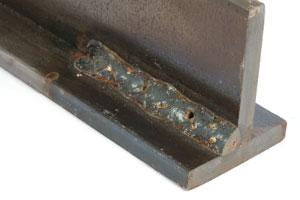
To detect and measure porosity, non-destructive testing approaches such as ultrasonic testing or X-ray assessment are often employed. These methods enable the identification of interior flaws without endangering the integrity of the weld. By analyzing the size, form, and circulation of porosity within a weld, welders can make informed decisions to improve their welding processes and accomplish sounder weld joints.
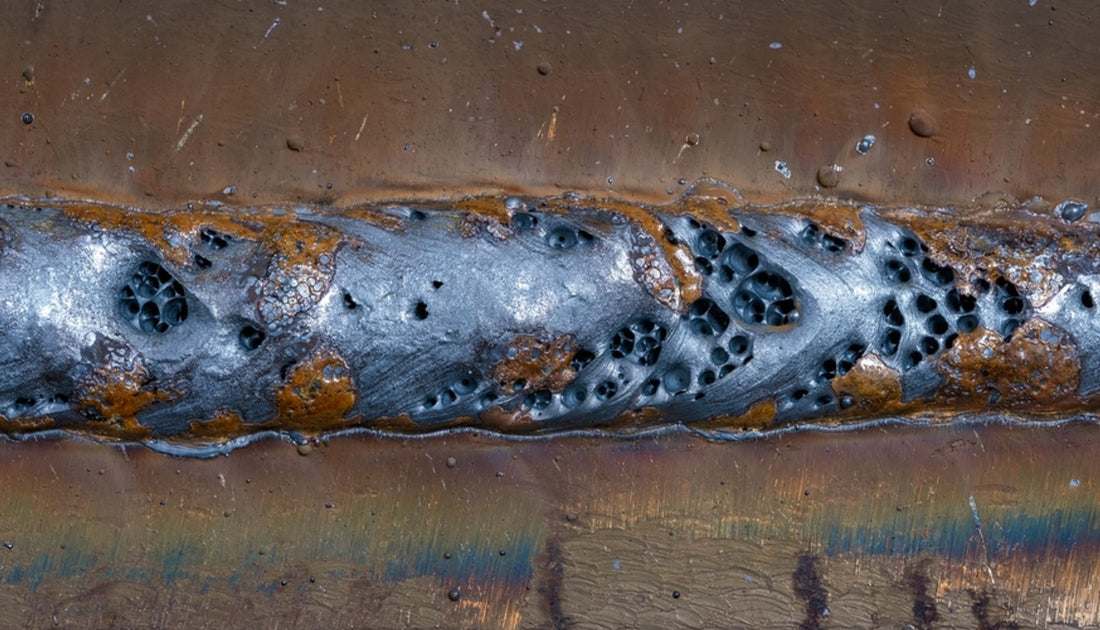
Elements Influencing Porosity Development
The occurrence of porosity in welding is affected by a myriad of variables, varying from gas protecting effectiveness to the ins and outs of welding parameter settings. Welding criteria, consisting of voltage, current, take a trip rate, and electrode kind, likewise impact porosity formation. The welding technique used, such as gas steel arc welding (GMAW) or protected steel arc welding (SMAW), can influence porosity formation due to variants in warm circulation and gas protection - What is Porosity.
Impacts of Porosity on Weld High Quality
The visibility of porosity additionally compromises the weld's resistance to corrosion, as the trapped air or gases within the spaces can react with the surrounding environment, leading to destruction over time. Additionally, porosity can prevent the weld's ability to withstand stress or impact, more endangering the overall top quality and reliability of the welded framework. In important applications such as aerospace, automotive, or structural building and constructions, where safety and security and sturdiness are critical, the detrimental impacts of porosity on weld high quality can have severe repercussions, emphasizing the relevance of reducing porosity via appropriate welding methods and procedures.
Methods to Minimize Porosity
To improve the quality of bonded joints and ensure structural integrity, welders and fabricators utilize details strategies intended at reducing the formation of gaps and dental caries within the material my sources throughout the welding procedure. One efficient approach to decrease porosity is to make sure proper product preparation. This consists of thorough cleaning of the base metal to get rid of any pollutants such as oil, grease, or moisture that can contribute to porosity formation. In addition, utilizing the appropriate welding parameters, such as the proper voltage, existing, and travel speed, is critical in avoiding porosity. Keeping a consistent arc size and angle throughout welding additionally aids minimize the chance of porosity.

Making use of the appropriate welding strategy, such as back-stepping or using a weaving movement, can also assist distribute warmth uniformly and lower the possibilities of porosity development. By applying these strategies, welders can successfully reduce porosity and produce high-quality bonded joints.

Advanced Solutions for Porosity Control
Carrying out advanced technologies and innovative techniques plays a pivotal function in accomplishing exceptional control over porosity in welding procedures. One sophisticated solution is the usage of advanced gas combinations. Protecting gases like helium or a mixture of argon and hydrogen can help in reducing porosity by giving much better arc security and boosted gas protection. In addition, employing sophisticated welding strategies such as pulsed MIG welding or customized ambience welding can also assist alleviate porosity problems.
Another advanced option involves making use of advanced welding tools. For example, making use of devices with integrated attributes like waveform control and sophisticated visit site power sources can improve weld top quality and decrease porosity dangers. The application of automated welding systems with precise control over parameters can considerably decrease porosity defects.
Furthermore, integrating innovative tracking and assessment innovations such as real-time X-ray imaging or automated ultrasonic testing can assist in discovering porosity early in the welding process, enabling immediate restorative activities. On the whole, incorporating these advanced remedies can substantially improve porosity control and boost the overall quality of bonded parts.
Conclusion
In verdict, understanding the This Site scientific research behind porosity in welding is essential for welders and fabricators to produce top notch welds - What is Porosity. Advanced remedies for porosity control can better improve the welding process and make sure a strong and dependable weld.